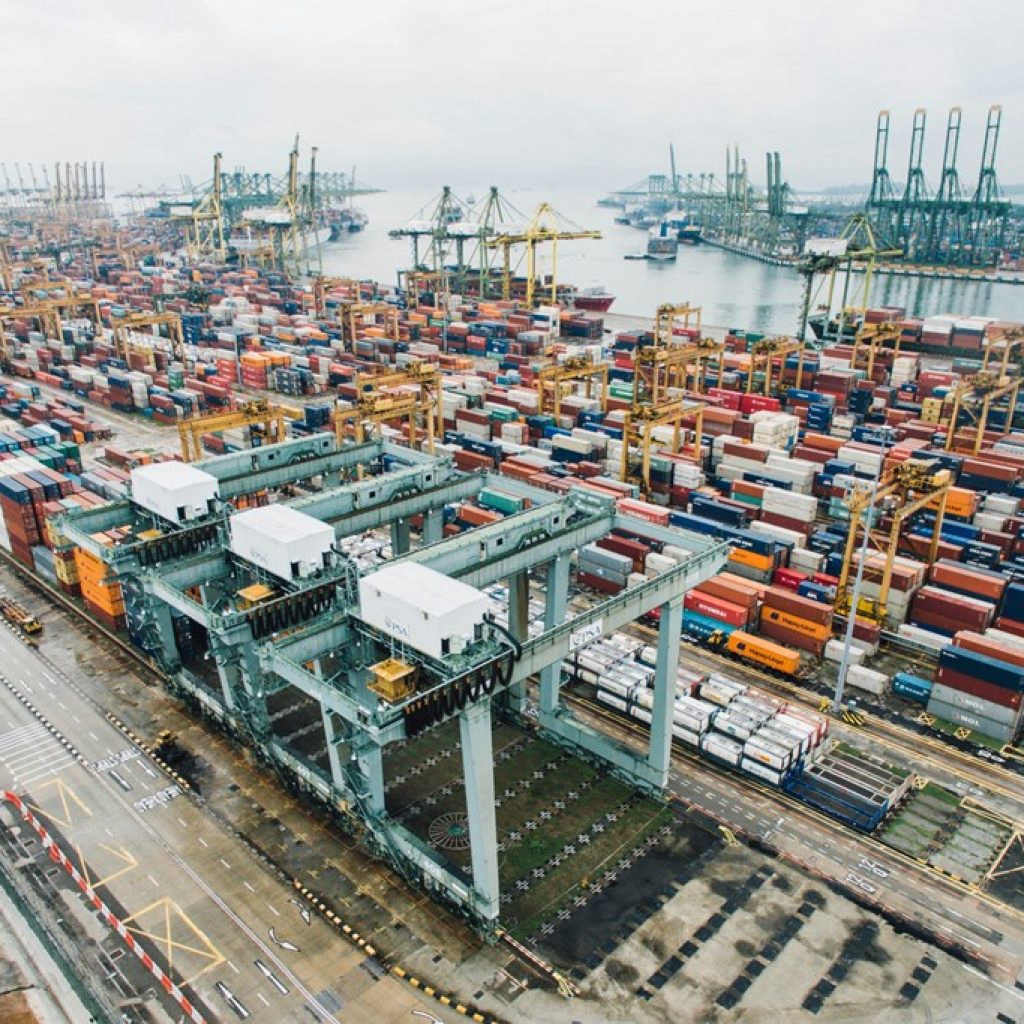
Purchasing management is an important aspect of a company’s operations. It has a direct impact on the company’s success and competitiveness in the marketplace. Effective organization allows to obtain the essential resources on the best terms, save money and ensure the smooth functioning of the business.
Procurement management: essence and significance
Procurement management is a set of activities and strategic decisions aimed at ensuring the supply of finished goods, materials and equipment for the production of products and services.This process includes the control of stock levels, prices of purchased goods and supplier relationships. The main goal of the enterprise is to ensure a continuous supply of the necessities to maintain the production process.
Common mistakes
Many companies follow outdated methods, which can slow down the production and affect competitiveness. Major negative factor is the lack of a procurement strategy. Chaotic procurement without a clear plan directly affects financial performance and increases company costs. Lack of motivation for the procurement department and lack of clear division of responsibility between departments has a negative impact.
Difficulties can also be caused by:
- insufficient qualification of employees in the procurement department;
- lack of coordination between departments;
- long contracts approval;
- insufficient level of management control.
Procurement control requires constant updating and optimisation as well as close monitoring.
The role of ERP efficiency for supply chain optimization
A comprehensive ERP software for supply chain allows you to control every step of the process with inbuilt analytical tools, quick access to data and flexible reporting.
- Demand identification
Identify the requirements for goods and services needed to produce the final product. At this stage, it is crucial to consider quantitative as well as qualitative parameters. A thorough needs analysis helps to avoid unnecessary costs and resource constraints.
- Analyzing existing stock
Update the current availability of goods and, if necessary, determine the quantity that needs to be procured. Helps to prevent overproduction.
- Supplier Selection
Select those who meet your company’s requirements. Concentrating on one supplier can bring bonuses and discounts, but there is a risk of supply disruption. Compare co-operative terms and prices from your multiple suppliers to make informed decisions and choose best options.
- Ensuring control over order fulfillment
Automating the ordering process helps to reduce time costs and improve the efficiency of the purchasing department. Enables continuous monitoring of suppliers’ compliance with deadlines and fulfillment of commitments. An effective order and payment monitoring system significantly reduces the risk and improves the procurement process.
- Receipt and inspection of goods
Once goods are received, they should be inspected. Return and replacement procedures are stipulated in the contract with the supplier and are integrated in the ERP module. You have a transparent procedure in case of receiving defective goods and products. It also provides tools to properly organize the storage of products in warehouses, taking into account their characteristics and safety requirements.
- Documentary support
Registration of incoming documents, transfer of payment for goods, resolution of possible disputes with suppliers. Correct fulfillment of all necessary documents contributes to the transparency of the process and reduces risks.
Coordinated actions in supply chain optimization with ERP software help to comply with business processes and avoid financial losses at all stages.
ERP for supply chain: a way to strengthen your business positioning
ERP solutions efficiency is becoming a key in supply chain management, enabling companies to adopt best practices. They help to streamline all processes and operations from planning to customer interaction, resulting in lower costs, better product quality and increased competitiveness.
The Procurement Management module helps to develop and strengthen relationships with suppliers. It gives the opportunity to establish long-term partnerships, leading to more favorable terms of cooperation, bonuses and discounts. The supply chain department gets operational control over the prices of purchased goods and raw materials. This allows companies to identify opportunities for cost reductions and more favorable agreements with suppliers.
The implementation of ERP systems requires a thorough approach and analysis of business needs, but the results justify the financial and time resources invested.